Total Quality Management (TQM) is a comprehensive approach to improving the quality and performance of organizational processes, products, and services. In the context of engineering projects, TQM can significantly enhance efficiency, reduce costs, and increase customer satisfaction.
This article explores the fundamental principles of TQM and outlines a step-by-step guide for its successful implementation in engineering projects.
Understanding Total Quality Management
TQM is a management philosophy that focuses on embedding quality in every aspect of an organization. It is built on the following key principles:
- Customer Focus: Understanding and meeting customer needs and expectations.
- Total Employee Involvement: Engaging all employees in quality improvement efforts.
- Process-Centered Approach: Emphasizing process management as a way to achieve consistent quality.
- Integrated System: Viewing the organization as a collection of interrelated processes.
- Strategic and Systematic Approach: Aligning quality initiatives with organizational goals.
- Continual Improvement: Committing to ongoing improvement in all areas.
- Fact-Based Decision Making: Using data and analysis to guide decisions.
- Communications: Maintaining open and effective communication channels within the organization.
Benefits of TQM in Engineering Projects
Implementing TQM in engineering projects offers numerous benefits:
- Enhanced Quality: Better adherence to specifications and standards.
- Increased Efficiency: Streamlined processes reduce waste and save time.
- Cost Reduction: Lower defect rates and rework costs.
- Improved Customer Satisfaction: Delivering higher quality products and services.
- Employee Satisfaction: A culture of quality can lead to greater job satisfaction and retention.
- Competitive Advantage: Higher quality can differentiate the organization in the marketplace.
Steps to Implement TQM in Engineering Projects
- Commitment from Top Management: Successful TQM implementation begins with a strong commitment from top management. Leaders must demonstrate their dedication to quality through their actions and decisions. This commitment should be communicated clearly throughout the organization.
- Develop a Quality Policy: Create a clear and concise quality policy that outlines the organization’s commitment to quality and continuous improvement. This policy should be aligned with the organization’s mission, vision, and strategic goals.
- Establish a Quality Management Team: Form a team responsible for driving TQM initiatives. This team should include representatives from various departments, including engineering, production, quality control, and human resources. The team will oversee the development and implementation of quality improvement plans.
- Conduct Training and Awareness Programs: Educate employees about TQM principles, tools, and techniques. Training programs should be tailored to different levels of the organization, ensuring that everyone understands their role in the quality improvement process.
- Identify and Map Key Processes: Identify the critical processes that impact the quality of engineering projects. Use tools like process mapping and flowcharts to visualize these processes and identify areas for improvement. Understanding these processes is crucial for managing and enhancing them effectively.
- Set Quality Objectives and Performance Metrics: Define specific, measurable, achievable, relevant, and time-bound (SMART) quality objectives. These objectives should be aligned with customer requirements and organizational goals. Establish performance metrics to monitor progress toward these objectives.
- Implement Process Improvement Initiatives: Apply quality improvement tools and techniques such as Six Sigma, Lean, and Kaizen to address identified process inefficiencies and defects. Encourage cross-functional collaboration and use data-driven approaches to solve problems.
- Develop a Robust Quality Assurance System: Implement a comprehensive quality assurance (QA) system to monitor and control quality throughout the project lifecycle. This system should include regular inspections, audits, and testing to ensure compliance with standards and specifications.
- Engage in Continuous Improvement: Foster a culture of continuous improvement by encouraging employees to identify and suggest improvements. Use techniques like PDCA (Plan-Do-Check-Act) cycles to systematically test and implement changes.
- Evaluate and Recognize Performance: Regularly evaluate the effectiveness of TQM initiatives through performance reviews and feedback. Recognize and reward employees and teams that contribute significantly to quality improvement. This recognition can motivate further participation and engagement.
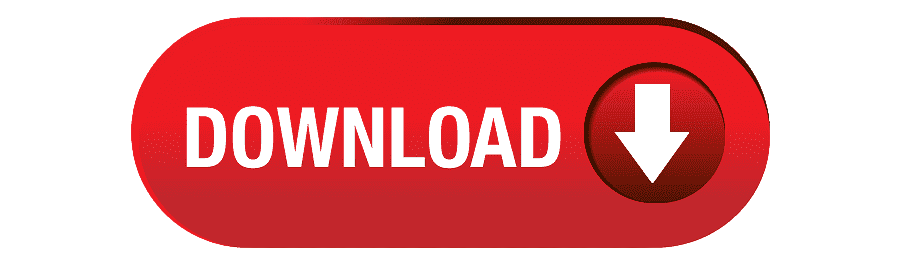
Challenges and Solutions in TQM Implementation
Challenges:
Solutions:
Conclusion
Implementing Total Quality Management in engineering projects is a strategic approach that can lead to significant improvements in quality, efficiency, and customer satisfaction. By adhering to TQM principles and following a structured implementation process, organizations can foster a culture of continuous improvement and achieve sustainable success. The journey towards TQM requires commitment, collaboration, and perseverance, but the benefits far outweigh the challenges.
The following are some selected Industry Courses to start today!
1. ISO MANAGEMENT SYSTEMS IMPLEMENTATION & INTERNAL AUDITOR COURSES
2. ISO LEAD AUDITOR COURSES
3. MANUFACTURING, QUALITY, PRODUCT DEVELOPMENT, OPERATIONS & SUPPLY CHAIN MANAGEMENT