Total Productive Maintenance (TPM) is an innovative approach to manufacturing that focuses on both production and equipment efficiency. It brings together production, maintenance, and engineering teams to create a cohesive system of equipment maintenance to improve production output. Originating in Japan, TPM has been hailed for its ability to reduce breakdowns, improve worker productivity, and foster a culture of continuous improvement.
History and Origins
TPM was developed in the 1960s and evolved from Preventive Maintenance (PM) practices used in the United States. Japan's need for maximizing the efficiency of their existing equipment due to resource constraints provided a fertile ground for TPM to evolve. Japanese manufacturers combined PM practices with their unique workplace management methodologies, thus giving birth to TPM.
Key Principles of TPM
- Holistic Involvement: One of TPM's unique features is the involvement of all staff, from top management to frontline operators. Everyone participates in proactive maintenance activities.
- Zero Goals: The ultimate objective is achieving the following:
- Zero defects
- Zero breakdowns
- Zero accidents
- Ongoing Training: Continuous training ensures that all employees have the necessary skills to carry out their TPM duties.
- Proactive Maintenance: This principle emphasizes preventing breakdowns before they happen rather than just reacting to them. It involves regularly inspecting and servicing equipment to ensure it's in optimal working condition.
- Root Cause Analysis: When problems do occur, TPM requires a thorough investigation into the root cause, not just fixing the immediate issue.
The Eight Pillars of TPM
The methodology of TPM is built upon eight supporting pillars:
- Autonomous Maintenance: This involves training operators to manage minor maintenance tasks, freeing up skilled maintenance teams to work on more complex issues.
- Planned Maintenance: Regularly scheduled maintenance tasks ensure machines are always in optimal working condition.
- Quality Maintenance: Focusing on ensuring equipment produces goods to the required quality standards.
- Focused Improvement: Small teams work together to solve specific issues, leading to continuous incremental improvements.
- Early Equipment Management: This pillar focuses on designing new equipment to require minimal maintenance and have long productive lives.
- Training and Education: Ensuring all staff have the skills they need, both in their specific roles and in the broader understanding of TPM.
- Safety, Health, Environment: Prioritizing safety and health in all TPM activities.
- Administrative & Office TPM: Extending TPM methodologies to office functions, ensuring the entire organization is streamlined and efficient.
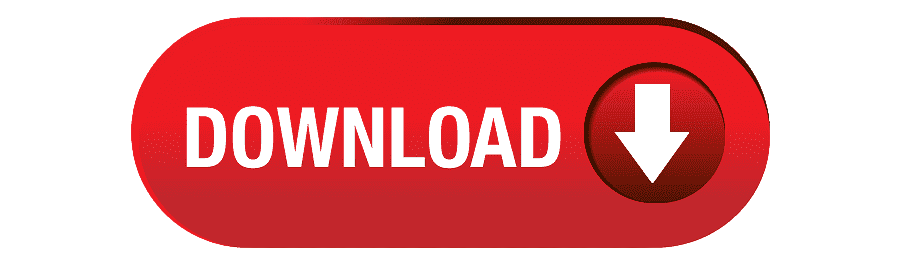
Benefits of TPM
Adopting TPM can lead to numerous benefits:
- Increased Operational Efficiency: Through reduced breakdowns and defects.
- Higher Product Quality: Machines that are well-maintained tend to produce better, more consistent products.
- Improved Employee Morale: As everyone is involved and invested in the process, leading to a sense of ownership and pride.
- Reduced Costs: Through better use of equipment, reduced wastage, and fewer breakdowns.
Conclusion
Total Productive Maintenance is a comprehensive and strategic approach to maintaining and improving production systems. It's not just about fixing machines; it's about fostering a culture of continuous improvement, collaboration, and proactive maintenance. Organizations that successfully implement TPM can expect to see significant improvements in production efficiency, product quality, and overall profitability.