In the dynamic environment of modern businesses, quality management is crucial for maintaining competitive advantage, ensuring customer satisfaction, and improving operational efficiency. One of the effective tools used in the domain of quality management is Quantitative Force Field Analysis (QFFA). This method provides a systematic approach to analyzing the forces that affect organizational change, particularly those impacting quality initiatives. By quantifying these forces, organizations can make informed decisions that enhance the effectiveness of their quality management systems.
Understanding Force Field Analysis
Force Field Analysis (FFA) was originally developed by Kurt Lewin, a social psychologist, as a tool to understand the dynamics of organizational change. It is based on the premise that any situation is maintained by a balance between driving forces that push for change and restraining forces that resist change. In the context of quality management, these forces can be internal or external factors that either support or hinder the implementation of quality initiatives.
Quantitative Force Field Analysis: An Overview
Quantitative Force Field Analysis builds on Lewin’s original concept by assigning numerical values to the driving and restraining forces. This quantification allows for a more precise assessment of the situation and helps prioritize the actions needed to achieve desired quality outcomes.
The process typically involves the following steps:
- Identify the Change Objective: Clearly define the quality improvement goal or the specific change that is being analyzed.
- List the Driving and Restraining Forces: Identify all the factors that will drive the change (e.g., customer demands, regulatory requirements, technological advancements) and those that will restrain it (e.g., lack of resources, resistance to change, inadequate training).
- Assign Weights to Each Force: Evaluate the strength of each force on a scale (e.g., 1 to 5 or 1 to 10), with higher numbers indicating stronger forces.
- Calculate the Net Force: Sum the values of the driving forces and restraining forces separately. The net force is determined by subtracting the total restraining forces from the total driving forces.
- Analyze the Results: If the net force is positive, it indicates that the driving forces outweigh the restraining forces, suggesting a higher likelihood of successful change implementation. Conversely, a negative net force suggests significant resistance to change, requiring strategic interventions to strengthen driving forces or reduce restraining forces.
- Develop Action Plans: Based on the analysis, devise strategies to enhance driving forces and mitigate or eliminate restraining forces. This may involve stakeholder engagement, training programs, resource allocation, or process optimization.
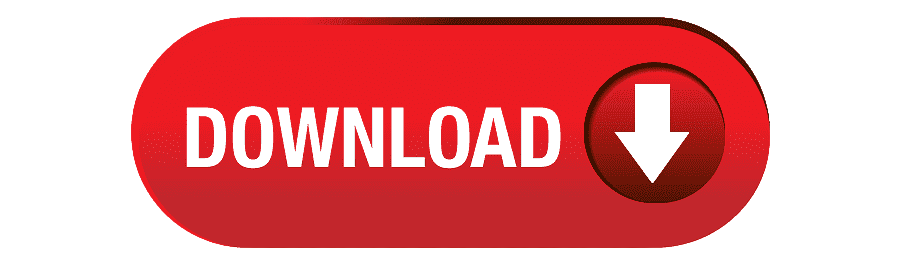
Applications of QFFA in Quality Management
Quantitative Force Field Analysis can be applied in various aspects of quality management, including:
- Process Improvement Initiatives: When implementing new quality processes or improving existing ones, QFFA helps identify potential challenges and supports the development of effective strategies to overcome them.
- Quality Assurance Programs: In quality assurance, QFFA can be used to evaluate the factors influencing product quality, ensuring that the most critical aspects are addressed to meet customer and regulatory requirements.
- Six Sigma and Lean Projects: QFFA can be integrated into Six Sigma and Lean methodologies to quantify the forces impacting process variability and waste reduction efforts, thereby enhancing the effectiveness of these initiatives.
- Change Management in Quality Systems: When transitioning to new quality management systems (QMS) or updating existing ones, QFFA assists in identifying the forces that may affect the success of the transition and enables better planning and execution.
Case Study: QFFA in a Manufacturing Quality Improvement Initiative
Consider a manufacturing company aiming to reduce defect rates in its production process. The quality management team decides to implement an advanced statistical process control (SPC) system.
Step 1: Identify the Change Objective
- The objective is to implement SPC to reduce defect rates by 30% within six months.
Step 2: List the Driving and Restraining Forces
- Driving Forces:
- Customer demand for higher quality (8/10)
- Availability of SPC technology (7/10)
- Management support (6/10)
- Restraining Forces:
- Resistance from operators due to lack of SPC knowledge (8/10)
- Initial cost of SPC implementation (7/10)
- Potential disruption during implementation (5/10)
Step 3: Assign Weights to Each Force
- Driving Forces Total: 21
- Restraining Forces Total: 20
Step 4: Calculate the Net Force
- Net Force = 21 (Driving Forces) - 20 (Restraining Forces) = +1
Step 5: Analyze the Results
- The net force of +1 indicates a slight advantage towards successful implementation, but the closeness of the total scores suggests that the restraining forces are almost as strong as the driving forces.
Step 6: Develop Action Plans
- Enhance the driving forces by providing SPC training to operators, securing additional funding to cover initial costs, and developing a detailed implementation plan to minimize disruptions.
Benefits of Quantitative Force Field Analysis in Quality Management
- Structured Decision-Making: QFFA provides a structured approach to decision-making, allowing quality managers to systematically assess the factors influencing change and make informed decisions.
- Prioritization of Actions: By quantifying the forces, QFFA helps prioritize actions that will have the most significant impact on achieving quality objectives.
- Enhanced Stakeholder Engagement: QFFA involves the identification and assessment of forces from various stakeholders, fostering a collaborative approach to quality improvement.
- Risk Mitigation: By identifying restraining forces early in the process, QFFA enables organizations to anticipate and mitigate potential risks that could derail quality initiatives.
Challenges and Limitations
While QFFA is a powerful tool, it is not without challenges:
- Subjectivity in Weighting Forces: Assigning numerical values to forces can be subjective, potentially leading to biased results. It requires the involvement of experienced and knowledgeable personnel to ensure accuracy.
- Complexity in Large-Scale Applications: In large organizations with numerous driving and restraining forces, the analysis can become complex, requiring sophisticated tools and methods to manage.
- Dependence on Accurate Data: The effectiveness of QFFA depends on the availability of accurate and relevant data to assess the forces accurately.
Conclusion
Quantitative Force Field Analysis is an invaluable tool in quality management, offering a systematic and quantifiable approach to understanding the dynamics of change. By analyzing and prioritizing the forces that influence quality initiatives, organizations can develop effective strategies to achieve their quality objectives. Despite its challenges, when applied correctly, QFFA can significantly enhance the decision-making process, leading to more successful quality management outcomes.
Industry Courses to start today!
1. MANUFACTURING, QUALITY, PRODUCT DEVELOPMENT, OPERATIONS & SUPPLY CHAIN MANAGEMENT
2. ISO MANAGEMENT SYSTEMS IMPLEMENTATION & INTERNAL AUDITOR COURSES
3. ISO LEAD AUDITOR COURSES