We help you reap the benefits of satisfying your customers through process improvements and provision of systems and tools that enables you provide best quality products and services via application of principles and methodologies in...
- QA/QC, Production & Maintenance
- Lean Management
- Lean Six Sigma
- Total Quality Management etc.
We help set up laboratories, recommend quality assurance tools, processes, methods and novel equipment that enable organizations meet and exceed their customers' needs and expectations at all time.
We assist organization in managing all of their suppliers’ programs and quality control projects including Supplier Planning, Product Design Qualification, New Product Introduction, Manufacturing Quality Control, Sustainability and Improvement.
Supplier Planning
We assist organization
- Create supply plans to ensure availability of raw materials
- Evaluate suppliers and determining the effectiveness customers’ multiple supplier strategies
- Identify supply chain risks and mitigation steps
- Analyze inventories to determine how to improve inventory turns, reduce waste, and optimize customer service
Product Design Qualification
We assist organization streamline new product launches, thereby enabling concurrent planning and product development, reducing time-to-manufacture and improving efficiency. This we do by ensuring that
- Ensuring that vendors provide the resources to support product development projects
- Interfacing with vendors on production readiness and fulfillment
- Handling packaging instructions and artwork
- Production monitoring of engineering build
- Testing against regulatory requirements
- Verifying reliability
- Designing change management
Manufacturing Quality Control
We ensure high product quality through continuous communication, consistent control, and a strong design in the quality control standards and methodologies shared with outsourced vendors, making sure that our customers’ products are always delivered at a consistent level of quality. We do this through
- Quality review of suppliers’ work
- Close collaboration with clients to update and implement changes to quality processes and criteria
- Tracking, measuring, and reporting quality metrics
- Driving continuous quality improvement programs
- Process standardization, monitoring cost, and driving process efficiencies
- Issuing daily, weekly, and monthly reports
- Identifying and reviewing opportunities for continuous improvement of operations
- Implementing failure analysis, root cause analysis, and corrective action
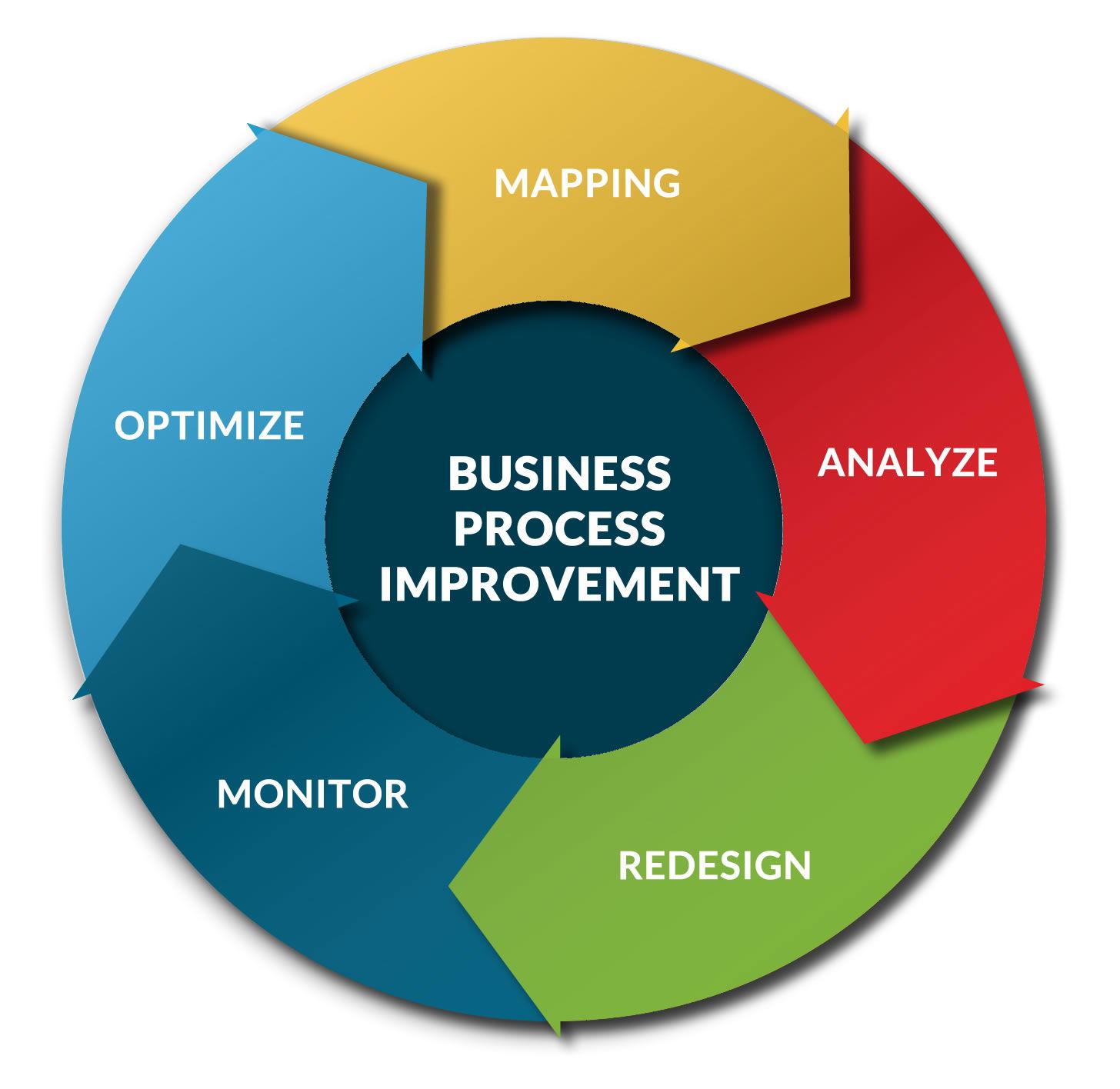
You can also check out our Quality Management resources via the link: