Good Manufacturing Practices (GMP) is a collection of principles and guidelines that ensure the consistent production and control of products, mainly in the pharmaceutical and food industries. One critical aspect of GMP is the concept of Change Control Management. This article delves into what change control management is, its significance, and how it plays a pivotal role in ensuring product quality and safety.
What is Change Management?
Change Management refers to the systematic approach to managing all changes made to a product or system. It is a formalized process that ensures that any proposed changes are reviewed, approved, implemented, and documented in a controlled manner. This process is designed to prevent unintended consequences that might compromise product quality, safety, or regulatory compliance.
Why is Change Control Important in GMP?
- Ensuring Product Quality and Safety: Any change, whether it relates to raw materials, equipment, processes, or even personnel, can potentially impact the final product's quality. A controlled change process ensures that these changes do not inadvertently introduce defects or inconsistencies.
- Regulatory Compliance: Regulatory bodies worldwide mandate that manufacturers implement a robust change control system. It not only ensures product safety and efficacy but also facilitates transparency and traceability in manufacturing processes.
- Minimizing Risk: An efficient change control system identifies potential risks associated with proposed changes, enabling organizations to assess and mitigate them before implementation.
- Documentation and Traceability: Change control processes ensure that all changes are documented appropriately. This documentation is crucial during audits, recalls, or any investigations.
Key Elements of Change Management in GMP
- Initiation: Any change starts with a proposal. This could be due to a corrective action, an improvement initiative, or adapting to new regulations. The rationale and the scope of the change are documented.
- Risk Assessment: Before approving a change, its potential impact on the product's quality and safety must be evaluated. Risk assessment tools, such as Failure Mode and Effect Analysis (FMEA), can be employed.
- Review and Approval: Proposed changes are reviewed by a cross-functional team of experts. This ensures that the change is evaluated from multiple perspectives, including quality assurance, production, engineering, and regulatory affairs.
- Implementation: Once approved, the change is implemented. This might involve updating procedures, re-training staff, or modifying equipment.
- Verification and Validation: Post-implementation, it's essential to verify that the change has been correctly implemented and to validate that it has the intended effect without introducing new issues.
- Documentation: Every stage of the change control process, from initiation to closure, must be documented in detail. This provides a historical record and ensures transparency.
- Review: Periodically, the change control system itself should be reviewed to ensure its effectiveness and to identify areas for improvement.
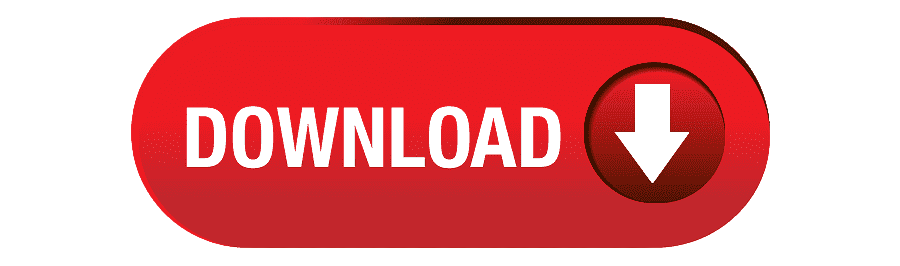
Challenges in Change Management
While the process might seem straightforward, there are challenges. These include:
- Ensuring that all personnel understand the importance of the process and adhere to it.
- Balancing the need for change with the potential risks.
- Maintaining a clear and comprehensive documentation trail.
- Ensuring efficient communication across various departments.
Conclusion
Change Control Management is a cornerstone of GMP. It ensures that any modifications in the product, process, or system are handled in a controlled and documented manner, ensuring consistent product quality and safety. With increasing scrutiny from regulatory bodies and the ever-present need for product quality, an effective change control system is more critical than ever.