In process engineering, controllers play a crucial role in maintaining the desired output of a system by adjusting the inputs based on feedback. Different types of controllers are used depending on the nature of the process, desired control performance, and specific requirements of the system. This article provides an overview of the main types of controllers used in process engineering, including Proportional (P), Integral (I), Derivative (D), Proportional-Integral (PI), Proportional-Derivative (PD), Proportional-Integral-Derivative (PID), and advanced control strategies.
1. Proportional (P) Controller
Description
A Proportional controller adjusts the control signal in proportion to the error, which is the difference between the setpoint and the process variable. The control law is given by:
u(t)=Kpe(t)
where u(t) is the control signal, Kp is the proportional gain, and e(t) is the error.
When to Use
- Simple systems where the dynamics are straightforward.
- Processes where a steady-state offset can be tolerated.
- Systems that require a quick response.
Advantages
- Easy to implement and tune.
- Provides a fast response to changes in setpoint or disturbances.
Disadvantages
- Steady-state error (offset) is present.
- High gain can lead to instability.
2. Integral (I) Controller
Description
An Integral controller eliminates the steady-state error by integrating the error over time. The control law is:
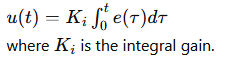
When to Use
- Systems where eliminating steady-state error is crucial.
- Processes that are relatively slow and where quick response is not critical.
Advantages
- Eliminates steady-state error.
Disadvantages
- Can lead to slow response.
- May cause instability and oscillations if not properly tuned.
3. Derivative (D) Controller
Description
A Derivative controller predicts the future trend of the error by considering its rate of change. The control law is:
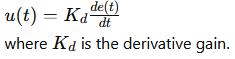
When to Use
- Processes with rapid changes or oscillations.
- Systems where anticipating the future trend of the error improves control.
Advantages
- Improves stability and damping.
- Reduces overshoot and oscillations.
Disadvantages
- Sensitive to noise in the error signal.
- Does not eliminate steady-state error.
4. Proportional-Integral (PI) Controller
Description
A PI controller combines the proportional and integral actions to provide both quick response and elimination of steady-state error. The control law is:

When to Use
- Systems that require quick response and elimination of steady-state error.
- Processes with moderate dynamics.
Advantages
- Eliminates steady-state error.
- Provides a balance between responsiveness and stability.
Disadvantages
- Tuning can be more complex than P or I controllers.
- May lead to slower response compared to a P controller alone.
5. Proportional-Derivative (PD) Controller
Description
A PD controller combines proportional and derivative actions to provide both quick response and improved stability. The control law is:

When to Use
- Systems that require quick response and improved damping.
- Processes with rapid changes or oscillations.
Advantages
- Improves stability and reduces overshoot.
- Provides quick response.
Disadvantages
- Does not eliminate steady-state error.
- Sensitive to noise.
Description
A PID controller combines all three actions: proportional, integral, and derivative. The control law is:

When to Use
- Complex systems with significant dynamic changes.
- Processes that require precise control and minimal steady-state error.
Advantages
- Eliminates steady-state error.
- Improves stability and response time.
- Versatile and widely applicable.
Disadvantages
- Tuning can be complex and time-consuming.
- Sensitive to noise in the derivative term.
7. Adaptive Controllers
Description: Adaptive controllers modify their parameters automatically in real-time to adapt to changing process conditions.
Working Principle:
- Continuously adjusts the controller parameters based on feedback from the process.
- Uses algorithms to identify changes in the process and adapt the control strategy accordingly.
Applications:
- Processes with varying dynamics
- Systems subject to frequent disturbances
- Advanced aerospace applications
Advantages:
- Flexible and can handle process variability
- Reduces the need for manual retuning
Disadvantages:
- More complex and computationally intensive
- Requires sophisticated algorithms and implementation
8. Fuzzy Logic Controllers
Description: Fuzzy logic controllers use fuzzy logic rather than binary logic to handle imprecise or uncertain information.
Working Principle:
- Uses fuzzy sets and rules to map inputs to outputs.
- Mimics human decision-making by handling partial truths.
Applications:
- Non-linear and complex systems
- HVAC systems
- Robotics
Advantages:
- Robust in handling imprecision and uncertainty
- Can be easier to design for complex systems
Disadvantages:
- May require more computational resources
- Designing fuzzy rules and membership functions can be complex
9. Model Predictive Controllers (MPC)
Description:
Model Predictive Controllers use a model of the process to predict future outputs and optimize control actions.
Working Principle:
- Uses a mathematical model to predict future behavior of the process.
- Solves an optimization problem at each control interval to determine the control action.
Applications:
- Chemical and petrochemical processes
- Multivariable control systems
- Processes with constraints on inputs and outputs
Advantages:
Disadvantages:
- Computationally intensive
- Requires an accurate process model
10. Neural Network Controllers
Description: Neural Network Controllers use artificial neural networks to learn and adapt to process dynamics.
Working Principle:
- Trained using historical process data.
- Adjusts control actions based on learned patterns and real-time feedback.
Applications:
- Complex non-linear systems
- Systems with unknown dynamics
- Adaptive control in dynamic environments
Advantages:
- Capable of handling non-linear and complex systems
- Can learn and adapt over time
Disadvantages:
- Requires significant training data
- Computationally intensive and complex to design
Conclusion
Selecting the right controller in process engineering is essential for achieving optimal performance and stability. Proportional, Integral, and Derivative controllers provide fundamental control actions that can be combined to suit various process requirements. Advanced control strategies like MPC, adaptive control, fuzzy logic, and neural network control offer enhanced performance for complex and dynamic systems. The choice of controller depends on the specific characteristics of the process, desired control objectives, and practical considerations such as implementation complexity and computational resources.
Some Selected Industry Courses to start today!
1. ISO MANAGEMENT SYSTEMS IMPLEMENTATION & INTERNAL AUDITOR COURSES
2. ISO LEAD AUDITOR COURSES
3. MANUFACTURING, QUALITY, PRODUCT DEVELOPMENT, OPERATIONS & SUPPLY CHAIN MANAGEMENT