The 14 Points for the Transformation of Management was Dr. W. Edwards Deming’s guide for organizational leadership to enable them use their leadership roles to improve the quality of their products and/or services and, overall effectiveness of their organization. These points are coined from Dr. Deming’s book, titled ‘’Out of the Crisis’’.
TrainingKeeper V3 Software
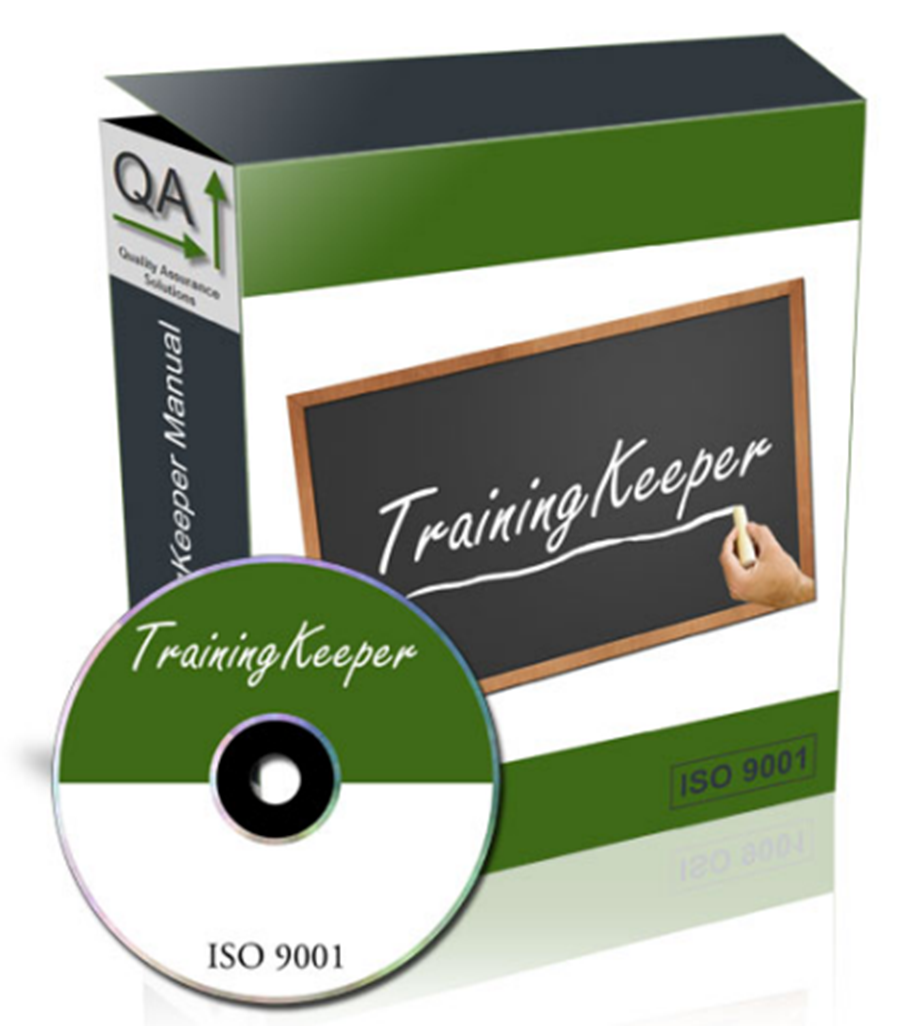
- Clarity of Purpose: Create constancy of purpose toward improvement of product and service, with the goal of becoming and remaining competitive, and to provide jobs.
- Lead the Change: Adopt new philosophies and way of doing things in a regularly changing economy. Management must awaken to the challenge, learn and understanding their responsibilities in times of change.
- Discourage Dependence on Inspection: Dependence on inspection to achieve quality should be discouraged. This to be done by eliminating the need for inspection on a mass basis by building quality into the product in the first place.
- Don’t Focus Merely on Price: Discontinue the practice of awarding business merely on the basis of price tag. Instead, minimize total cost. Rather, gradually move toward a single supplier for any one item, on a long-term relationship of loyalty and trust.
- Strive After Perfection: Constantly and forever improve the system of production and service, so as to improve quality and productivity with the result of constantly decreasing costs.
- Train on The Job: Institute on-the-job training.
- Institute & Ensure leadership: The primary objective of supervision should be to help people and machines and gadgets perform better. This point out the fact that supervision of management is in need of overhaul, as well as supervision of shop floor workers.
- Never Rule by Fear: Discourage and drive out fear, so that everyone can work effectively for the company.
- Remove Barriers: Cut off barriers between departments so that everyone can work as team. People in research, design, sales and production must work as a team, to foresee problems of production and in use that may be encountered with the product or service.
- Remove Targets: Eliminate slogans, exhortations and targets for the work force asking for zero defects and new levels of productivity. Such targets only create adversarial relationships, as the bulk of the causes of low quality and low productivity belong to the system and thus lie beyond the power of the work force.
- Eliminate work standards on the shop floor, substituting it with leadership.
- Eliminate management by objective. Eliminate management by numbers, numerical goals, substituting them with leadership.
- Promote Pride of Workmanship: Remove barriers that rob the hourly worker of their right to pride of workmanship. The focus of supervisors must be changed from mere numbers to quality.
- Discontinue Merit Ratings: Remove barriers that rob people in management and engineering to their right to pride of workmanship, meaning, inter alia, abolishment of the annual or merit rating and of management by objectives.
- Offer Continuous Learning Opportunities: Institute a vigorous program of education and self-improvement.
- Work Together: Everybody in the company is to work together to accomplish the transformation. The transformation is everybody’s job.
Download FREE ebook on Paperless Quality Management here.
Download this FREE Presentation Guide in PPT
Download this FREE if you a fresher in Quality Management.
Adebayo is a thought leader in continuous process improvement and manufacturing excellence. He is a Certified Six Sigma Master Black Belt (CSSMBB) Professional and Management Systems Lead Auditor (ISO 9001, 45001, ISO 22000/FSSC 22000 etc.) with strong experience leading various continuous improvement initiative in top manufacturing organizations.
You can reach him here.