ISO 9001 is an internationally recognized standard for Quality Management Systems (QMS) aimed at helping organizations ensure consistent quality in their products and services. Implementing ISO 9001 involves a systematic approach, including documentation of various processes and procedures. These documents serve as a roadmap for organizations to achieve and maintain compliance with the standard. Understanding the mandatory document requirements is crucial for a successful ISO 9001 implementation.
- Quality Policy: The quality policy is a fundamental document that outlines the organization's commitment to quality and customer satisfaction. It should be concise, easily understood, and endorsed by top management. The policy should reflect the organization's objectives and serve as a guide for decision-making at all levels.
- Quality Manual: While ISO 9001:2015 no longer requires a formal quality manual, many organizations still find it beneficial to create one. A quality manual provides an overview of the organization's QMS, including its scope, documented procedures, and interaction of processes. It helps stakeholders understand the structure and implementation of the QMS.
- Documented Procedures: ISO 9001 mandates the documentation of certain procedures to ensure consistency and control in various processes. These procedures may include:
a. Control of documents: Procedures for creating, reviewing, approving, and updating documents to ensure their accuracy and relevance.
b. Control of records: Guidelines for the identification, storage, protection, retrieval, retention, and disposition of records to demonstrate conformity to requirements.
c. Internal audit: Procedures for planning, conducting, and reporting internal audits to verify the effectiveness of the QMS and identify areas for improvement.
d. Corrective and preventive actions (CAPA): Processes for addressing nonconformities, taking corrective actions to eliminate root causes, and implementing preventive measures to prevent recurrence.
- Process Maps and Flowcharts: Visual representations of key processes and their interactions help stakeholders understand how activities are performed within the organization. Process maps and flowcharts can identify inputs, outputs, responsibilities, and sequence of activities, aiding in process improvement and risk management.
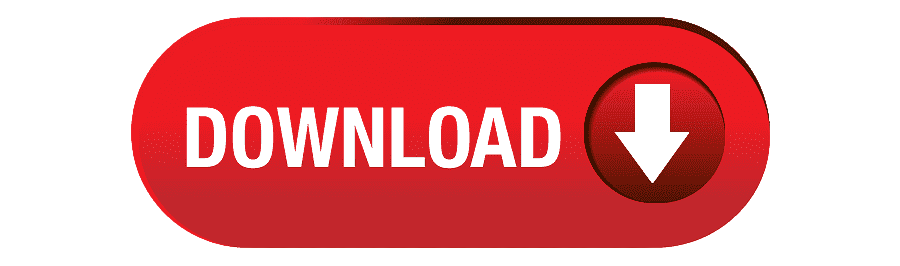
- Work Instructions: Detailed instructions specifying the steps to perform tasks or activities are essential for ensuring consistency and quality. Work instructions may include safety precautions, equipment operation, quality checkpoints, and other relevant information to guide employees in their roles.
- Quality Records: Documentation of evidence that processes are being performed as planned and that requirements are being met is critical for ISO 9001 compliance. Quality records may include inspection reports, test results, customer feedback, training records, and nonconformity reports, among others.
- Risk Management Documentation: ISO 9001:2015 emphasizes the importance of risk-based thinking in quality management. Organizations are required to identify and address risks and opportunities that could affect the QMS and its ability to achieve intended results. Documentation of risk assessments, risk treatment plans, and monitoring activities is essential for effective risk management.
Conclusion
Implementing ISO 9001 requires careful documentation of various processes, procedures, and records to ensure compliance with the standard's requirements. These documents serve as a framework for establishing and maintaining an effective QMS that consistently delivers quality products and services. By understanding and fulfilling the mandatory document requirements, organizations can reap the benefits of ISO 9001 certification, including improved customer satisfaction, enhanced process efficiency, and competitive advantage in the marketplace.
Click HERE to download or any of the following process improvement products:
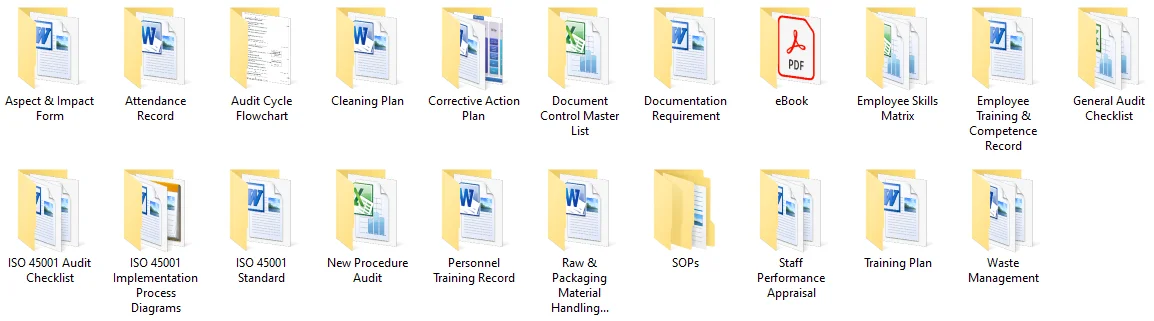
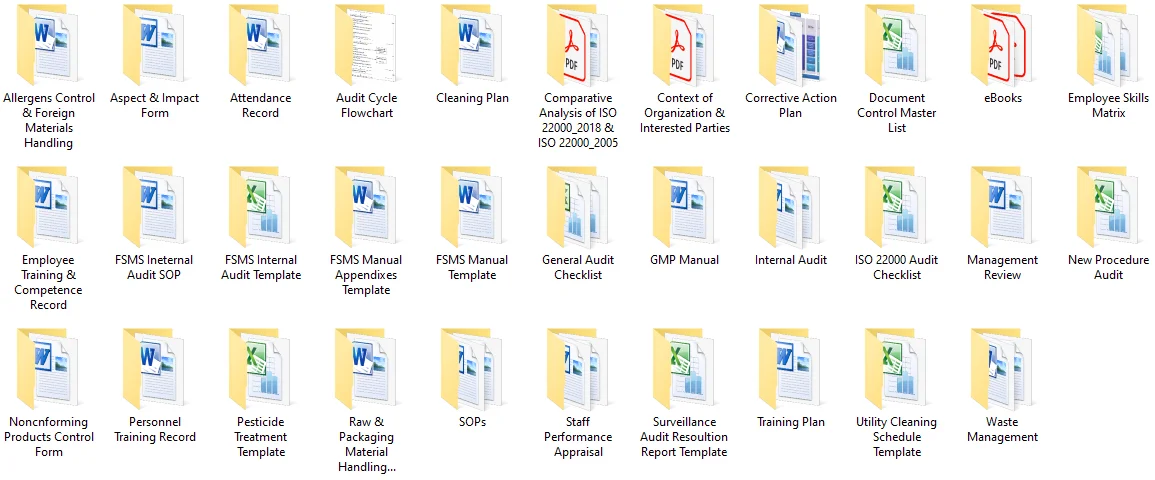
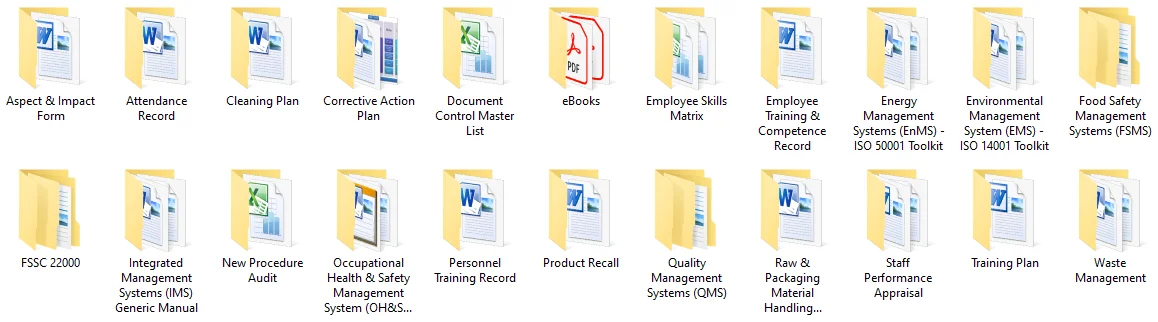
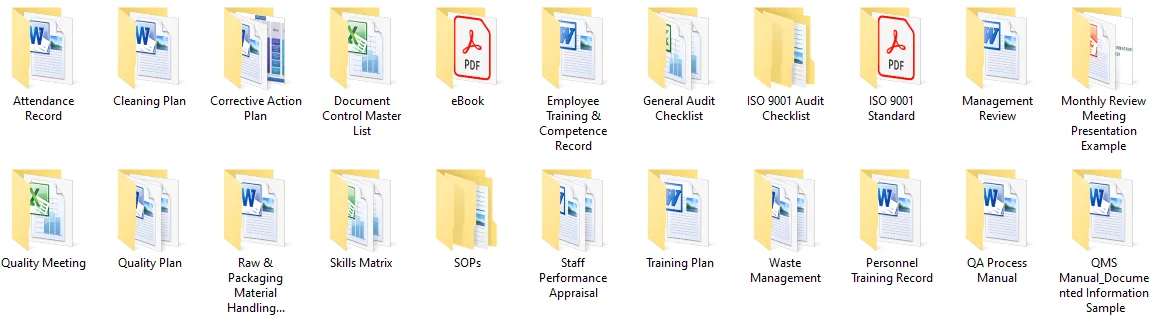
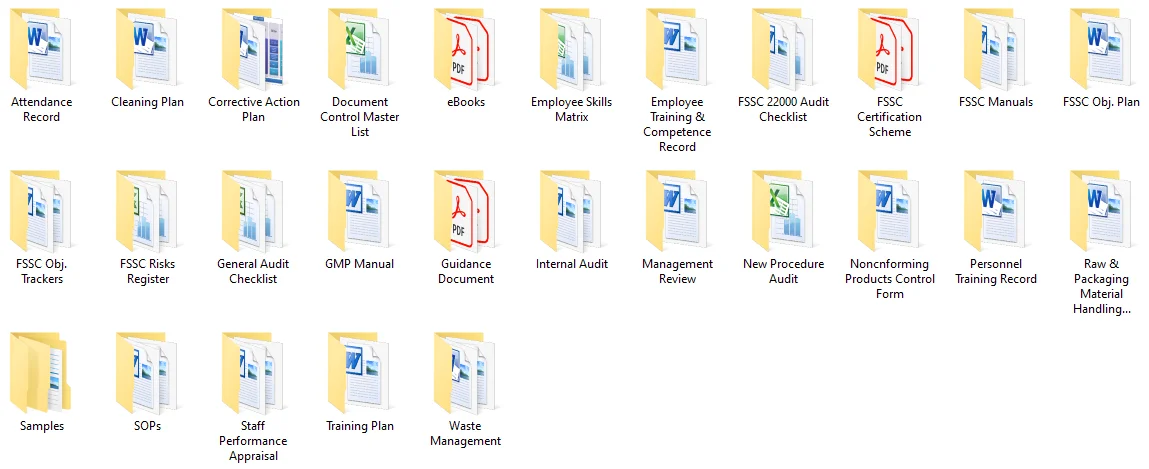
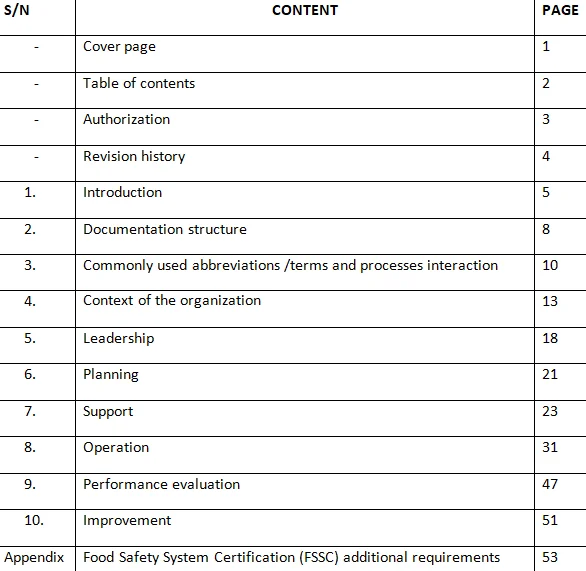

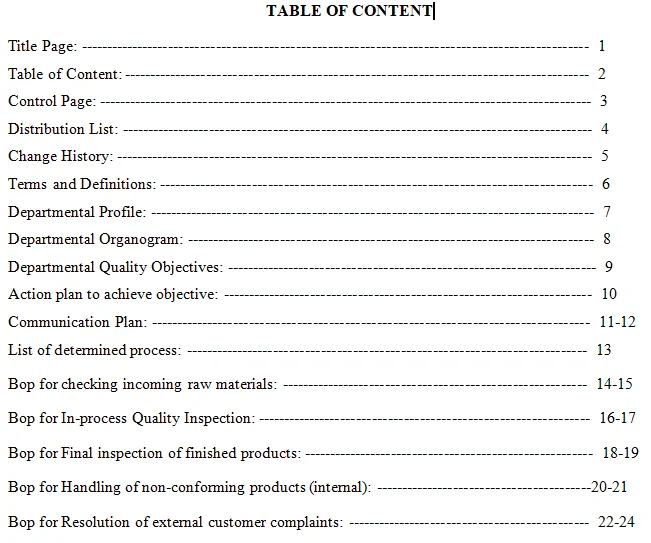