Good Manufacturing Practices (GMP) are a set of guidelines and regulations that govern the manufacturing processes of pharmaceuticals, ensuring that they are safe, effective, and of high quality. One crucial aspect of GMP compliance is documentation and record-keeping. Effective documentation and record-keeping are essential for ensuring the safety and efficacy of products. This article explores the significance of GMP documentation and record-keeping in the pharmaceutical industry.
The Importance of GMP Documentation
- Traceability and Accountability: GMP documentation provides a comprehensive and traceable record of every step in the manufacturing process. This includes raw material procurement, equipment calibration, batch processing, and quality control testing. This level of traceability is crucial in identifying and addressing any issues that may arise during production. If a problem occurs, such as a product recall or quality deviation, having detailed documentation allows manufacturers to trace the issue back to its source and take corrective action promptly.
- Quality Control: GMP documentation is instrumental in ensuring that the quality of pharmaceutical products remains consistent. It enables manufacturers to set, monitor, and maintain specific quality standards for their products. Without accurate documentation, it would be nearly impossible to monitor and maintain these standards effectively.
- Regulatory Compliance: Regulatory bodies, such as the U.S. Food and Drug Administration (FDA) and the European Medicines Agency (EMA), require pharmaceutical manufacturers to adhere to GMP regulations. In many cases, demonstrating compliance is contingent on maintaining accurate and comprehensive documentation. Failure to do so can result in regulatory actions, including fines, product recalls, and, in extreme cases, facility shutdowns.
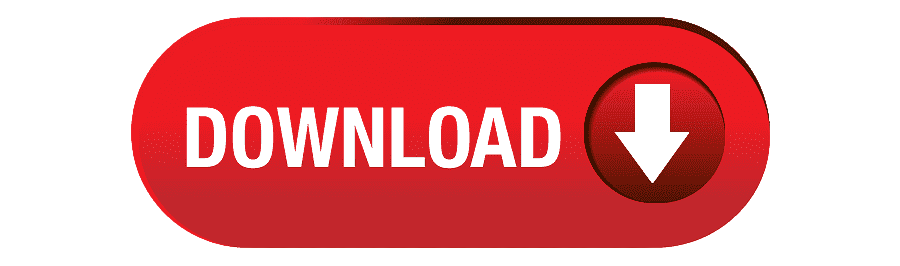
The Role of Record-Keeping in GMP Compliance
- Batch Records: Batch records are one of the most critical components of GMP documentation. These records provide a detailed account of each batch of pharmaceutical product produced. They include information on the manufacturing process, equipment used, personnel involved, raw material specifications, in-process testing, and final product testing. Batch records serve as a historical reference that can be used to verify the quality and consistency of products over time.
- Change Control Records: In a dynamic manufacturing environment, changes to equipment, processes, or materials are inevitable. Proper record-keeping of these changes is crucial to ensure that any alterations are made in a controlled and documented manner. Change control records capture the rationale for changes, the individuals responsible, and the associated validation and testing activities.
- Deviation Reports: In cases where deviations from established procedures occur, deviation reports are used to document the issue, its root cause, and the corrective and preventive actions taken. This documentation is critical for identifying and addressing the source of the problem to prevent its recurrence in the future.
- Equipment and Facility Maintenance Records: GMP compliance requires regular maintenance and calibration of manufacturing equipment and facilities. Records of these activities are essential to demonstrate that all equipment is operating within specified parameters, ensuring product quality and safety.
Best Practices for GMP Documentation and Record-Keeping
- Standard Operating Procedures (SOPs): Manufacturers must establish clear and well-documented SOPs for all critical processes. These SOPs serve as the foundation for GMP compliance, ensuring that personnel consistently follow established procedures.
- Training and Awareness: Proper training of personnel is crucial for effective GMP documentation and record-keeping. All employees should understand the importance of documentation, be aware of GMP requirements, and be trained in the use of record-keeping systems.
- Electronic Documentation Systems: Many manufacturing companies are transitioning to electronic documentation systems, which offer advantages in terms of efficiency, data security, and accessibility. However, these systems must be validated to ensure data integrity and security.
- Regular Audits and Inspections: Internal and external audits and inspections play a vital role in ensuring GMP compliance. Regular checks help identify gaps in documentation and record-keeping, allowing for corrective action.
Conclusion
GMP documentation and record-keeping are fundamental to the production of safe and effective pharmaceuticals. The pharmaceutical industry's strict regulatory environment demands precise and comprehensive documentation to guarantee the highest level of quality and safety for the products it manufactures. Accurate record-keeping is not only a regulatory requirement but also a best practice that ensures consistent product quality, traceability, and accountability throughout the manufacturing process. Pharmaceutical companies that prioritize GMP compliance and robust documentation will ultimately provide better products and protect public health.