Good Manufacturing Practices (GMP) are a set of essential guidelines and regulations that pharmaceutical companies must adhere to in order to ensure the quality, safety, and efficacy of their products. Compliance with GMP standards is vital for safeguarding public health and maintaining the integrity of the manufacturing industry. However, GMP non-compliance can occur due to various reasons, potentially leading to serious consequences for both companies and consumers.
In this article, we will explore the implications of GMP non-compliance and the corrective actions that manufacturers must take to address these issues effectively.
Understanding GMP Non-Compliance
GMP non-compliance refers to the failure of a manufacturer to meet the established GMP standards and regulations. This can encompass a wide range of violations, including but not limited to:
- Inadequate facilities and equipment: Manufacturing facilities must be designed, constructed, and maintained to meet GMP requirements. Non-compliance can occur when facilities are not up to standard or equipment is not properly calibrated or validated.
- Poor hygiene and sanitation: GMP mandates strict cleanliness and hygiene measures to prevent contamination. Non-compliance can result from insufficient cleaning procedures or improper sanitation practices.
- Inaccurate documentation: Proper record-keeping is crucial to trace and verify the manufacturing process. Non-compliance can occur if records are incomplete, inaccurate, or tampered with.
- Inadequate quality control: Manufacturers must implement robust quality control processes to ensure that products meet their specifications. Non-compliance can result from the lack of proper testing and quality control measures.
- Unauthorized process changes: Any changes in the manufacturing process must be properly documented and validated. Non-compliance can occur if unapproved changes are made without proper assessment.
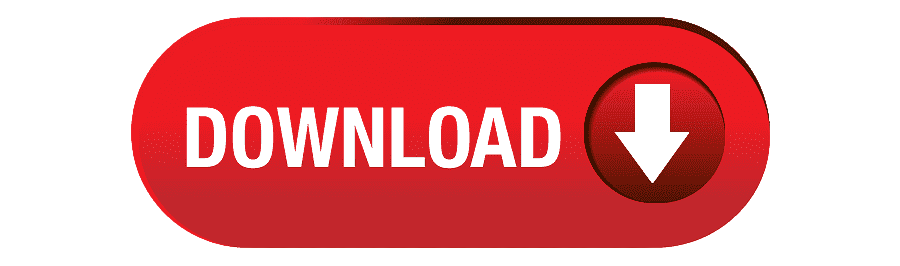
Implications of GMP Non-Compliance
GMP non-compliance has far-reaching consequences for pharmaceutical companies, consumers, and regulatory agencies. Some of the key implications include:
- Product quality and safety concerns: Non-compliance can lead to the production of substandard or unsafe pharmaceutical products, potentially harming patients and eroding trust in the pharmaceutical industry.
- Regulatory penalties: Regulatory bodies, such as the U.S. Food and Drug Administration (FDA) and the European Medicines Agency (EMA), can take punitive actions, including warning letters, fines, and product recalls, against non-compliant companies.
- Reputation damage: GMP non-compliance can severely damage a company's reputation, making it difficult to regain consumer and investor trust.
- Legal repercussions: Non-compliance can result in legal action, with potential liability for injuries or harm caused by substandard products.
Corrective Actions for GMP Non-Compliance
To address GMP non-compliance effectively and mitigate its consequences, pharmaceutical manufacturers must implement comprehensive corrective actions. Some critical steps to consider include:
- Immediate containment: When non-compliance is identified, manufacturers must take immediate action to prevent further production of non-compliant products. This may involve halting production, recalling products, or segregating non-compliant batches.
- Root cause analysis: Identifying the underlying causes of non-compliance is essential to prevent recurrence. Manufacturers should conduct thorough investigations to determine why the deviations occurred.
- Corrective actions: Once the root causes are identified, manufacturers should develop and implement corrective actions. These actions may involve process changes, equipment upgrades, and personnel training to address the specific issues that led to non-compliance.
- Preventive measures: In addition to correcting the immediate problems, pharmaceutical companies should also establish preventive measures to reduce the risk of non-compliance in the future. This may include revising procedures, enhancing quality control measures, and improving staff training.
- Communication with regulatory agencies: Companies should maintain open and transparent communication with regulatory authorities regarding the non-compliance issue, the corrective actions taken, and the preventive measures put in place.
- Ongoing monitoring and verification: After corrective actions are implemented, it is crucial to continuously monitor and verify compliance with GMP standards to ensure that the problems do not reoccur.
Conclusion
GMP non-compliance is a serious issue in the pharmaceutical industry that can have severe consequences for public health, regulatory compliance, and a company's reputation. To address non-compliance effectively, pharmaceutical manufacturers must follow a systematic approach that includes immediate containment, root cause analysis, corrective actions, preventive measures, and ongoing monitoring. By taking these steps, companies can safeguard product quality and safety, regain regulatory compliance, and rebuild trust with consumers and the industry as a whole.