Small to Medium Enterprises (SMEs) form the backbone of many global economies, driving innovation, employment, and economic growth. As these businesses strive to improve efficiency and remain competitive, they often face challenges, especially given their size and resources. One of the approaches SMEs can adopt to overcome these challenges is Lean Six Sigma.
What is Lean Six Sigma?
Lean Six Sigma is a process improvement methodology that combines the principles of Lean (focused on waste elimination) and Six Sigma (focused on reducing variation and defects). When implemented correctly, it can lead to significant operational improvements and cost savings.
Why is Lean Six Sigma Important for SMEs?
- Cost Savings: SMEs often operate on tight budgets. Implementing Lean Six Sigma can identify inefficiencies and eliminate wasteful practices, leading to significant cost savings.
- Improved Quality: Six Sigma's focus on reducing defects ensures that the quality of products or services is enhanced, leading to better customer satisfaction.
- Operational Efficiency: Lean principles can streamline operations, ensuring that SMEs get more done in less time with fewer resources.
- Enhanced Employee Morale: Engaging employees in process improvement initiatives can boost morale and increase overall job satisfaction.
Steps to Implement Lean Six Sigma in SMEs
- Leadership Commitment: It starts at the top. Leadership must understand the value of Lean Six Sigma and commit resources to its successful implementation.
- Training: Depending on the needs and scale of the SME, employees can be trained as White Belts, Yellow Belts, Green Belts, or Black Belts in Six Sigma.
- Project Selection: Choose projects that align with business goals. For SMEs, it's important to focus on quick wins initially to gain momentum and demonstrate value.
- Implementation: Use the DMAIC (Define, Measure, Analyze, Improve, Control) or DMADV (Define, Measure, Analyze, Design, Verify) frameworks to guide your projects. These systematic approaches ensure that problems are adequately defined, root causes are identified, and solutions are tested and implemented effectively.
- Review & Audit: After the project's completion, regularly review the changes to ensure they are delivering the expected benefits. Make adjustments if necessary.
- Celebrate & Scale: Recognize the teams and individuals who made the improvement projects a success. Then, scale the learnings across other areas of the business.
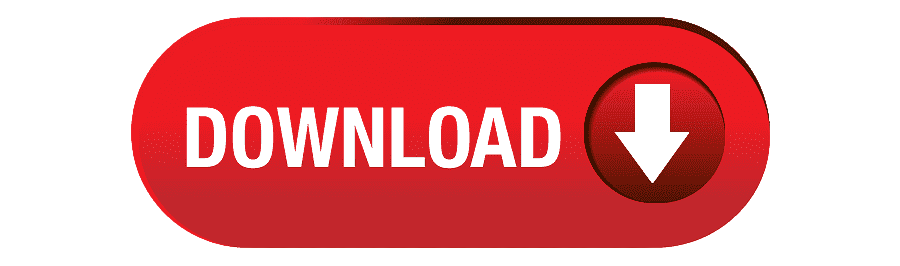
Potential Challenges
- Resistance to Change: Employees might be resistant to new ways of working or fear that efficiency improvements might lead to job losses.
- Lack of Resources: Given that SMEs often have fewer resources, dedicating time and manpower to Lean Six Sigma projects might seem challenging.
- Insufficient Training: Without adequate training, the methodology can be incorrectly applied, leading to subpar results.
To address these challenges, it's crucial to have strong leadership, ensure clear communication about the benefits of Lean Six Sigma, provide adequate training, and celebrate small wins to build momentum.
Conclusion
For SMEs looking to improve their operational efficiency, enhance product or service quality, and drive cost savings, Lean Six Sigma offers a robust framework. While the journey might be challenging, with commitment, training, and the right approach, SMEs can harness the power of Lean Six Sigma to secure a competitive edge in their markets.