Lean manufacturing is a systematic approach to optimizing processes and eliminating waste in manufacturing operations. It is a philosophy and methodology that has its roots in the Japanese manufacturing industry, particularly Toyota, where it was first developed in the 1950s. Since then, lean principles have been widely adopted by companies around the world to improve efficiency, reduce costs, and enhance product quality.
The core idea behind lean manufacturing is to create more value for customers with fewer resources. This is achieved by identifying and eliminating various forms of waste in the production process, including overproduction, waiting times, unnecessary transportation, excess inventory, motion, defects, and over-processing. By reducing or eliminating waste, companies can operate more efficiently, deliver products more quickly, and ultimately improve their bottom line.
Key Principles of Lean Manufacturing
- Value: Lean manufacturing starts with a clear understanding of what the customer values. This is often referred to as the "voice of the customer." By identifying what customers want and are willing to pay for, companies can focus their efforts on delivering that value while minimizing activities that do not contribute to it.
- Value Stream Mapping: A fundamental step in lean manufacturing is to map the entire value stream, which is the sequence of activities and processes required to deliver a product or service. This mapping helps identify areas where waste occurs and provides a visual representation of the current state of operations.
- Flow: Lean manufacturing promotes the concept of continuous flow, where products or components move smoothly and rapidly through the production process. By reducing interruptions, delays, and work-in-progress inventory, companies can increase efficiency and reduce lead times.
- Pull System: In lean manufacturing, the production process is driven by customer demand, known as a pull system. This means that products are only produced when they are needed, rather than being manufactured in anticipation of demand. This approach minimizes overproduction and reduces excess inventory.
- Just-in-Time (JIT): JIT is a key component of lean manufacturing, and it aims to deliver the right quantity of products at the right time to meet customer demand. By minimizing inventory and producing goods only when needed, companies can reduce carrying costs and respond more effectively to changes in demand.
- Continuous Improvement: Lean manufacturing is not a one-time initiative but an ongoing commitment to continuous improvement. The Kaizen philosophy, which means "change for better," is an integral part of lean manufacturing. It encourages employees at all levels to identify and implement small, incremental improvements in their work processes.
- Respect for People: Lean manufacturing recognizes the value of employees and their contributions to the organization. It encourages a culture of respect, teamwork, and empowerment, where employees are actively engaged in problem-solving and process improvement.
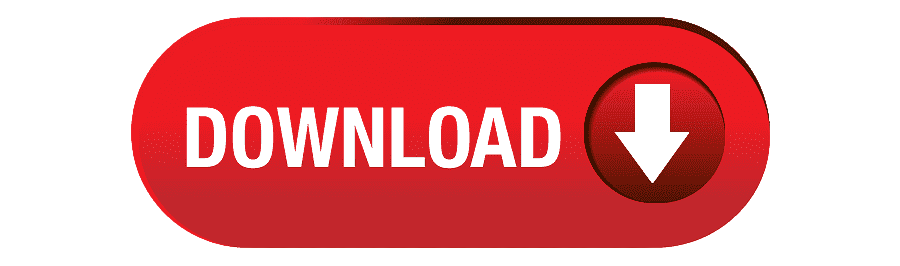
Benefits of Lean Manufacturing
Implementing lean manufacturing principles can lead to a wide range of benefits for companies, including:
- Increased Efficiency: Lean manufacturing streamlines processes and eliminates waste, resulting in improved productivity and reduced lead times.
- Cost Reduction: By minimizing inventory, reducing overproduction, and optimizing processes, companies can significantly lower operational costs.
- Improved Quality: Lean methodologies emphasize defect prevention and error reduction, leading to higher product quality.
- Greater Customer Satisfaction: Delivering products on time and meeting customer expectations can lead to higher levels of customer satisfaction and loyalty.
- Enhanced Employee Engagement: Lean principles encourage employees to participate in problem-solving and decision-making, fostering a sense of ownership and empowerment.
- Competitive Advantage: Lean manufacturing helps companies become more agile and responsive to market changes, giving them a competitive edge.
In conclusion, lean manufacturing is a powerful approach to improve efficiency, reduce waste, and enhance the quality of products and services. By focusing on the principles of value, continuous improvement, and a customer-centric approach, companies can optimize their operations and achieve sustainable success in an increasingly competitive business environment. Embracing lean manufacturing principles can lead to cost savings, increased customer satisfaction, and a more efficient and flexible organization.