ISO 10012-1:2003 is measurement management systems standard containing requirements for ensuring that measurements are made with intended accuracy. The standard contains all the necessary guidance on the implementation of the requirements. It also specifies the main features of the confirmation system. This management systems standard applies to measurement equipment used in the demonstration of conformance with a specification, not to other measuring equipment, records of measurement, or competence of personnel.
The standard applies to laboratories dedicated for testing, which include those providing a calibration service. It includes laboratories operating a quality system in accordance with ISO/IEC 17025 covering those who must meet the requirements of ISO 9001. ISO 10012 spelt out an integral part of the quality system which is the documentation of the control of inspection, measurement, and test equipment which must be specific in terms of which items of equipment are subject to the provisions, allocation of responsibilities, and actions to be taken.
The standard mandates that objective evidence must be available to validate that the required accuracy is achieved. This article lists some basic summaries of what must be accomplished to meet the requirements for a measurement quality system by ISO (and many other) standards. They include:
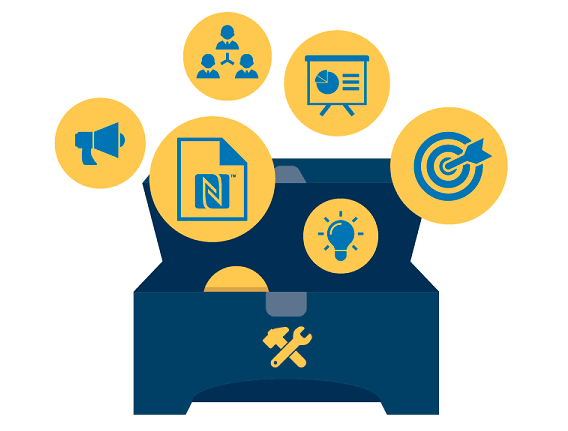
- Records and Documentation: All measuring equipment must be identified, controlled, and calibrated and records of the calibration and traceability to national standards must be kept. The methods and actions used to confirm the measuring equipment and devices must be documented.
- Development of SOPs: The system for evaluating measuring equipment to meet the required sensitivity, accuracy, and reliability must be defined in written procedures.
- Evaluation of Calibration System: The calibration system must be evaluated on a periodic basis by internal audits and by management reviews.
- Calibration Action Plan: The actions involved with the entire calibration system must be planned. This planning must consider management system analysis.
- Determination of Measurement Uncertainty: The uncertainty of measurement must be determined, which generally involves gage repeatability and reproducibility and other statistical methods.
- Retention Time of Records: Records must be kept on the methods used to calibrate measuring and test equipment and the retention time for these records must be specified.
- Handling of Nonconforming Products: Suitable procedures must be in place to ensure that nonconforming measuring equipment is not used.
Click for quality, lean, six sigma & ISO Management Systems courses
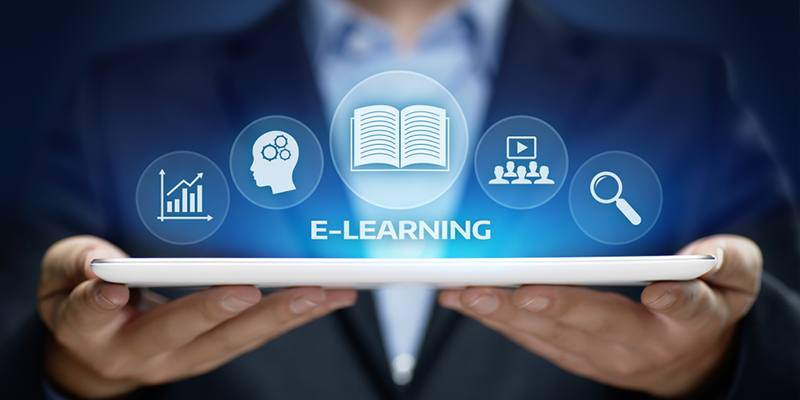
- Identification of Measuring Equipment: A labelling system must be in place that shows the unique identification of each piece of measuring equipment or device and its status.
- Calibration Frequency: The frequency of recalibration of measuring devices must be established, documented, and be based upon the type of equipment and severity of wear.
- Sealing of Adjusting Devices: Where adjustments may be made that may logically go undetected, sealing of the adjusting devices or case is required.
- Controls of External Calibration Services: Procedures must define controls that will be followed when any outside source is used regarding the calibration or supply of measuring equipment.
- Traceability of Calibration Systems: Calibrations must be traceable to national standards. If no national standard is available, the method of establishing and maintaining the standard must be documented.
- Handling of Measuring Equipment: Measuring equipment will be handled, transported and stored according to established procedures in order to prevent misuse, damage and changes in functional characteristics.
- Calculation of Uncertainties: Where uncertainties accumulate, the method of calculation of the uncertainty must be specified in procedures for each case.
- Storage Conditions of Measuring Equipment: Gages, measuring equipment, and test equipment will be used, calibrated, and stored in conditions that ensure the stability of the equipment. Ambient environmental conditions must be maintained.
- Procedures for Training Personnel: Documented procedures are required for the qualifications and training of personnel that make measurement or test determinations.
Adebayo is a thought leader in continuous process improvement and manufacturing excellence. He is a Certified Six Sigma Master Black Belt (CSSMBB) Professional and Management Systems Lead Auditor (ISO 9001, 45001, ISO 22000/FSSC 22000 etc.) with strong experience leading various continuous improvement initiative in top manufacturing organizations.
You can reach him here.