The 80/20 rule, also known as the Pareto Principle, suggests that roughly 80% of effects come from 20% of causes. This principle has found applications in various domains, including quality improvement processes within organizations. When applied to quality improvement, the 80/20 rule can offer several benefits, but it also comes with its limitations.
Benefits
- Focus on Critical Issues: One of the primary benefits of applying the 80/20 rule to quality improvement is that it helps organizations identify the critical few factors that contribute most significantly to quality issues. By focusing efforts on addressing these key issues, organizations can achieve significant improvements with relatively fewer resources.
- Efficient Resource Allocation: The 80/20 rule enables organizations to allocate resources more efficiently by prioritizing efforts on the vital few areas that yield the most significant impact on quality. This targeted approach prevents the wastage of resources on less critical factors, leading to cost savings and improved productivity.
- Quick Wins: Identifying and addressing the 20% of causes responsible for 80% of quality issues can lead to quick wins and visible improvements in a relatively short period. This not only boosts morale within the organization but also demonstrates the effectiveness of the quality improvement initiatives to stakeholders.
- Streamlined Processes: Focusing on the vital few factors allows organizations to streamline their processes by eliminating non-essential activities and optimizing workflows. This simplification can lead to smoother operations, reduced cycle times, and enhanced overall efficiency.
- Continuous Improvement Culture: The 80/20 rule encourages a culture of continuous improvement within organizations by emphasizing the importance of identifying and addressing key issues systematically. By regularly reassessing priorities and refining processes, organizations can sustain quality improvements over the long term.
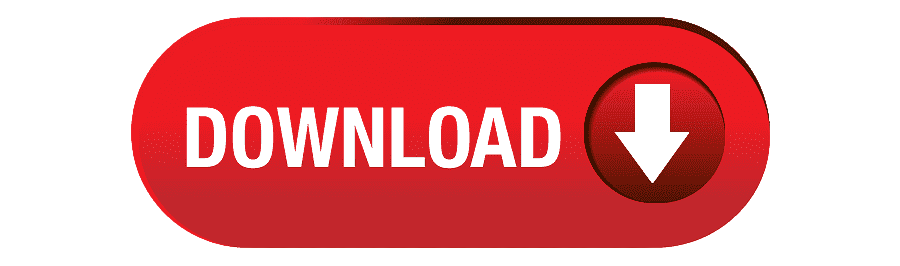
Limitations
- Simplistic Assumption: While the 80/20 rule provides a useful heuristic for prioritization, it is based on a simplistic assumption that may not always hold true in complex real-world scenarios. In some cases, the distribution of causes and effects may not follow the 80/20 ratio, leading to inaccurate prioritization.
- Lack of Context: The 80/20 rule does not consider the contextual factors that may influence the effectiveness of quality improvement initiatives. Factors such as industry-specific regulations, customer requirements, and organizational culture can significantly impact the relevance and applicability of the rule.
- Risk of Overlooking Minor Issues: Focusing solely on the vital few factors identified by the 80/20 rule may lead to the oversight of minor issues that, while individually less impactful, collectively contribute to overall quality degradation. Ignoring these smaller issues can undermine the effectiveness of quality improvement efforts in the long run.
- Resistance to Change: Implementing the 80/20 rule may face resistance from stakeholders who are accustomed to existing processes or reluctant to prioritize certain factors over others. Overcoming resistance to change requires effective communication, stakeholder engagement, and leadership support.
- Dynamic Nature of Quality: Quality improvement is an ongoing process that requires organizations to adapt to changing customer needs, market conditions, and technological advancements. The static nature of the 80/20 rule may limit its effectiveness in addressing evolving quality challenges over time.
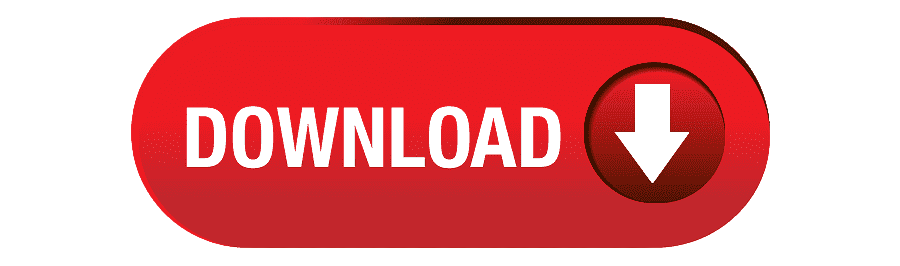
In conclusion, while the 80/20 rule offers several benefits for quality improvement, it is essential for organizations to recognize its limitations and use it as a guiding principle rather than a rigid formula. By combining the insights gained from the 80/20 rule with other quality management methodologies and continuous feedback mechanisms, organizations can develop more robust and adaptable approaches to improving quality and driving sustainable business success.
Click HERE to download or any of the following process improvement products:
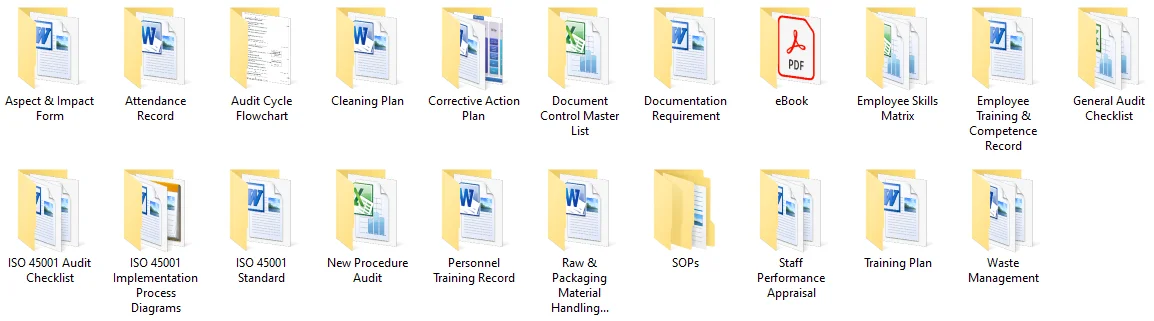
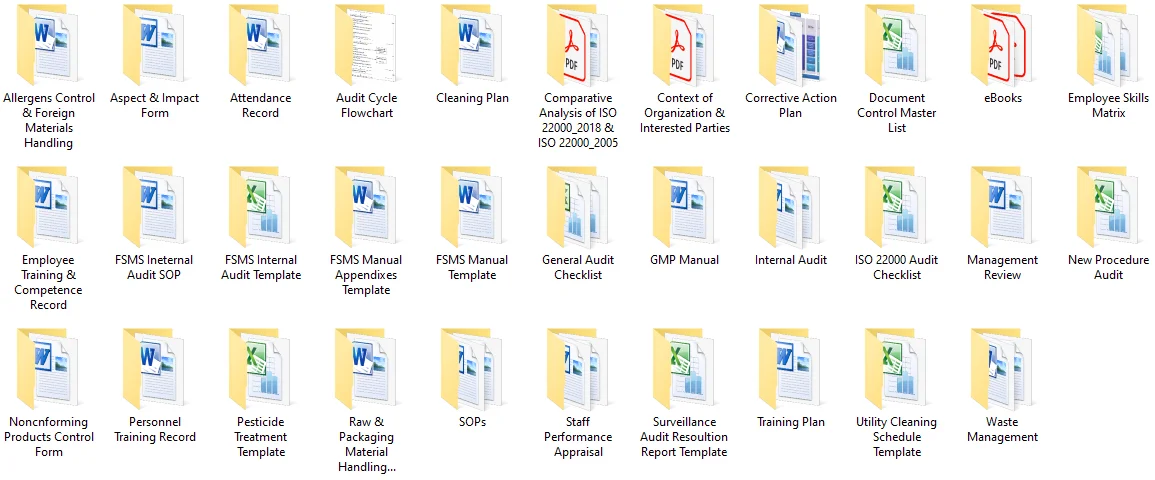
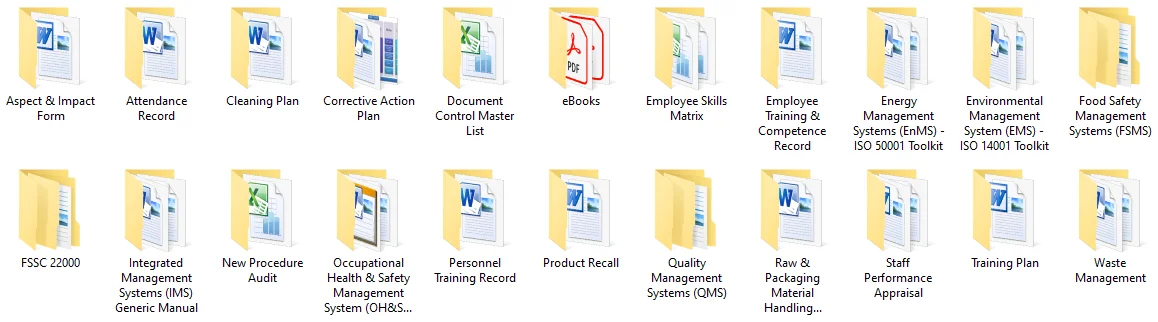
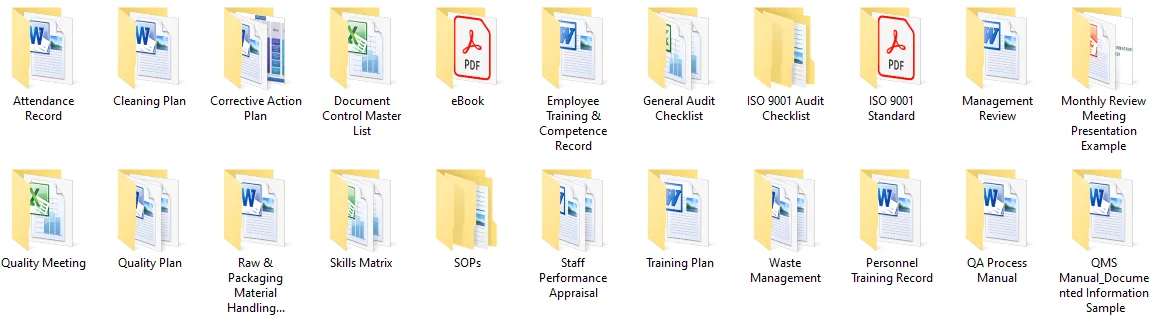
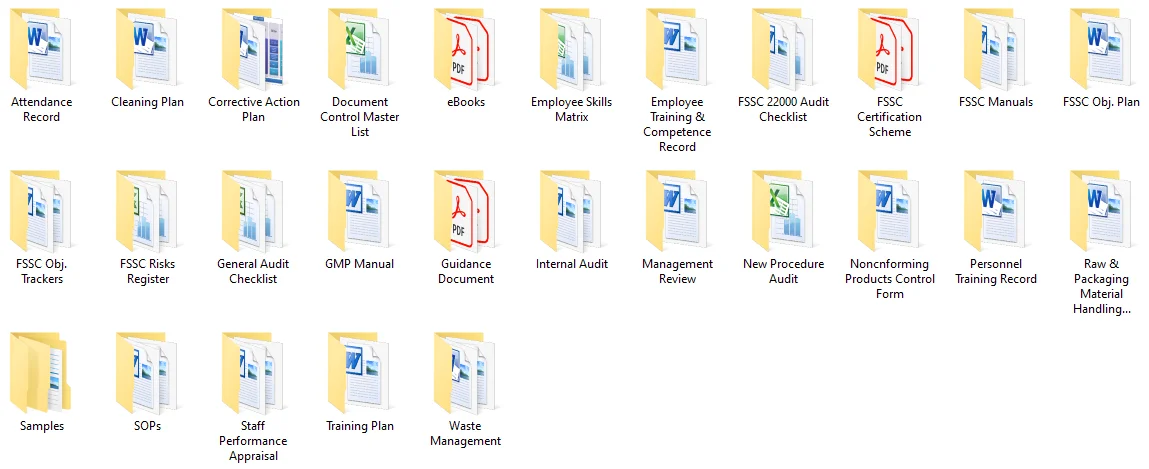
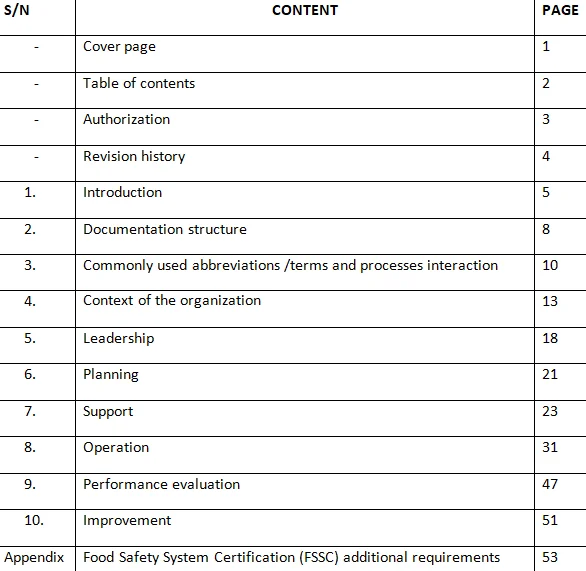

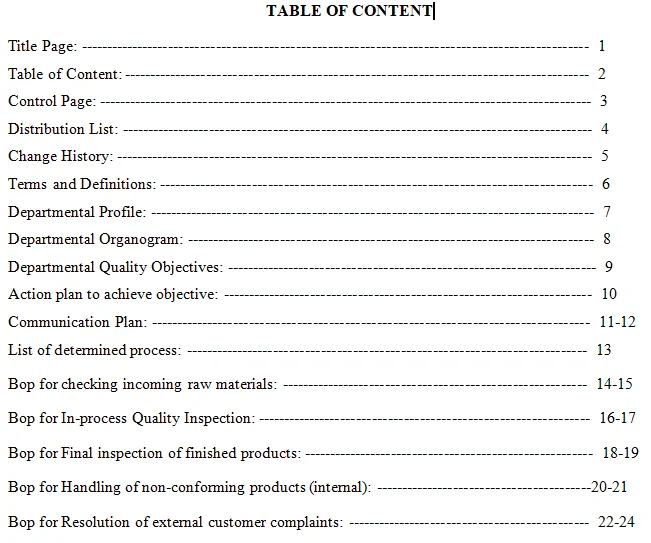